In an attempt to further my involvement with the Unmanned Aerial Systems program at Purdue University, I have been coming in over winter break to work on improving the lab. There are many things that can be improved, and what better way to learn about managing a UAS program then to actually work on improving the one you are already involved with. This also provided a great opportunity to learn some new skills. The first thing I began working on was revising the battery storage and charging setup within the UAS lab.
The UAS lab had an area for which batteries were kept, but it was away from the charging station, and was in the TA office, which at times is locked away from students. There was a need to create an organized system closer to the charging area for batteries to be held. The instructor I’ve had this past semester, William Weldon, suggested 3D printing inter-connectable holders for all of the DJI smart batteries. While I had no real previous 3D modeling or printing experience, I took on the task. Over the following week time frame I rapidly prototyped different holders for the Mavic 2 Pro, M210, and DJI controller batteries.
I started by finding an original Mavic Pro battery holder on the website Thingaverse. The general shape matched that of the Mavic 2 Pro batteries, however they are different dimensions. So, using a simple 3D modeling software, I took that design, measured out the dimensions of the Mavic 2 Pro Battery, and customized the base file to fit the intended battery. I exported this very first trial run as an STL file and put it into the manufacturer suggested 3D printing software called Cura. I then worked with Weldon to properly configure the printer settings to create a high-speed print for the purpose of testing the scaling changes I made.
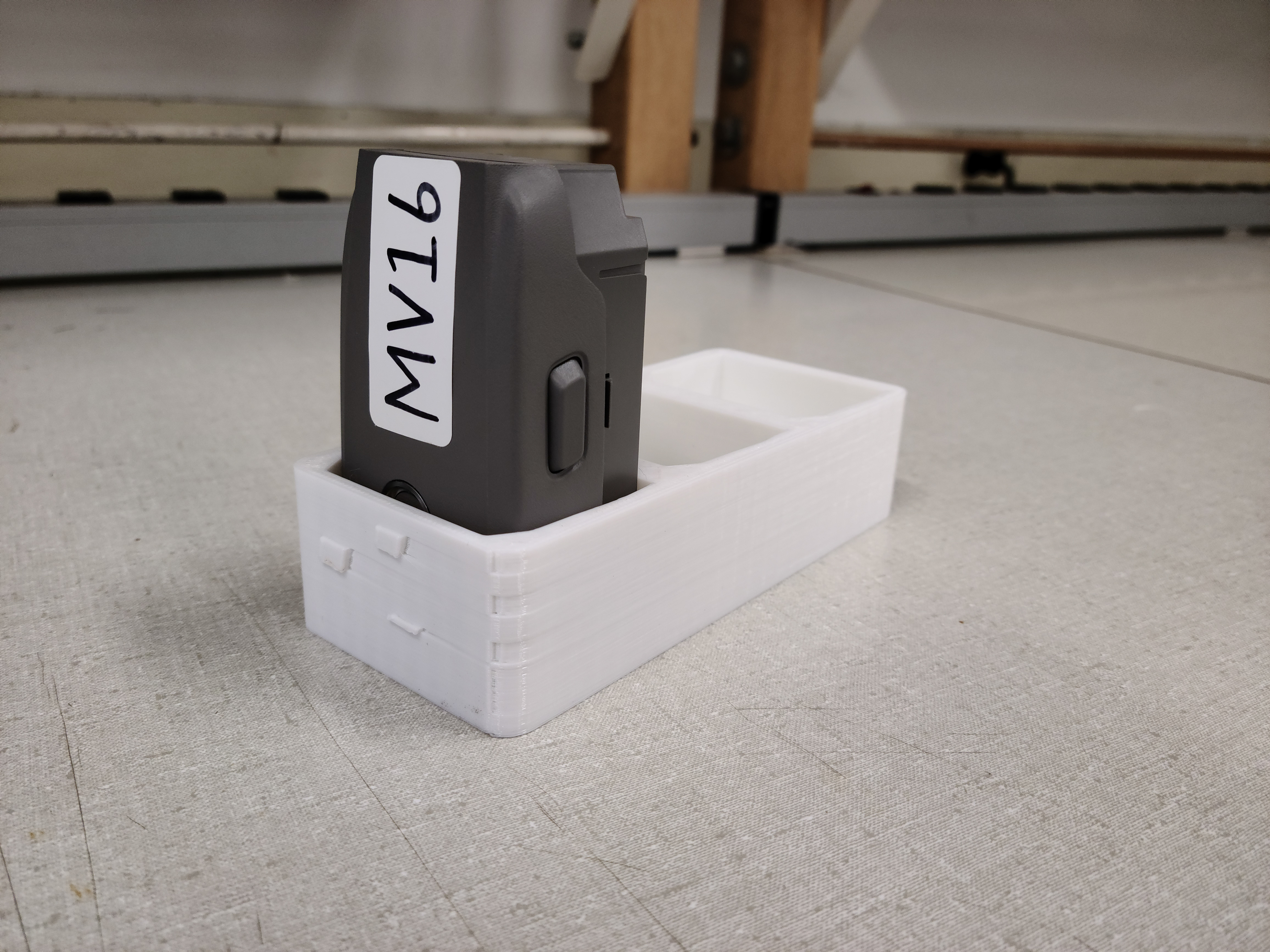
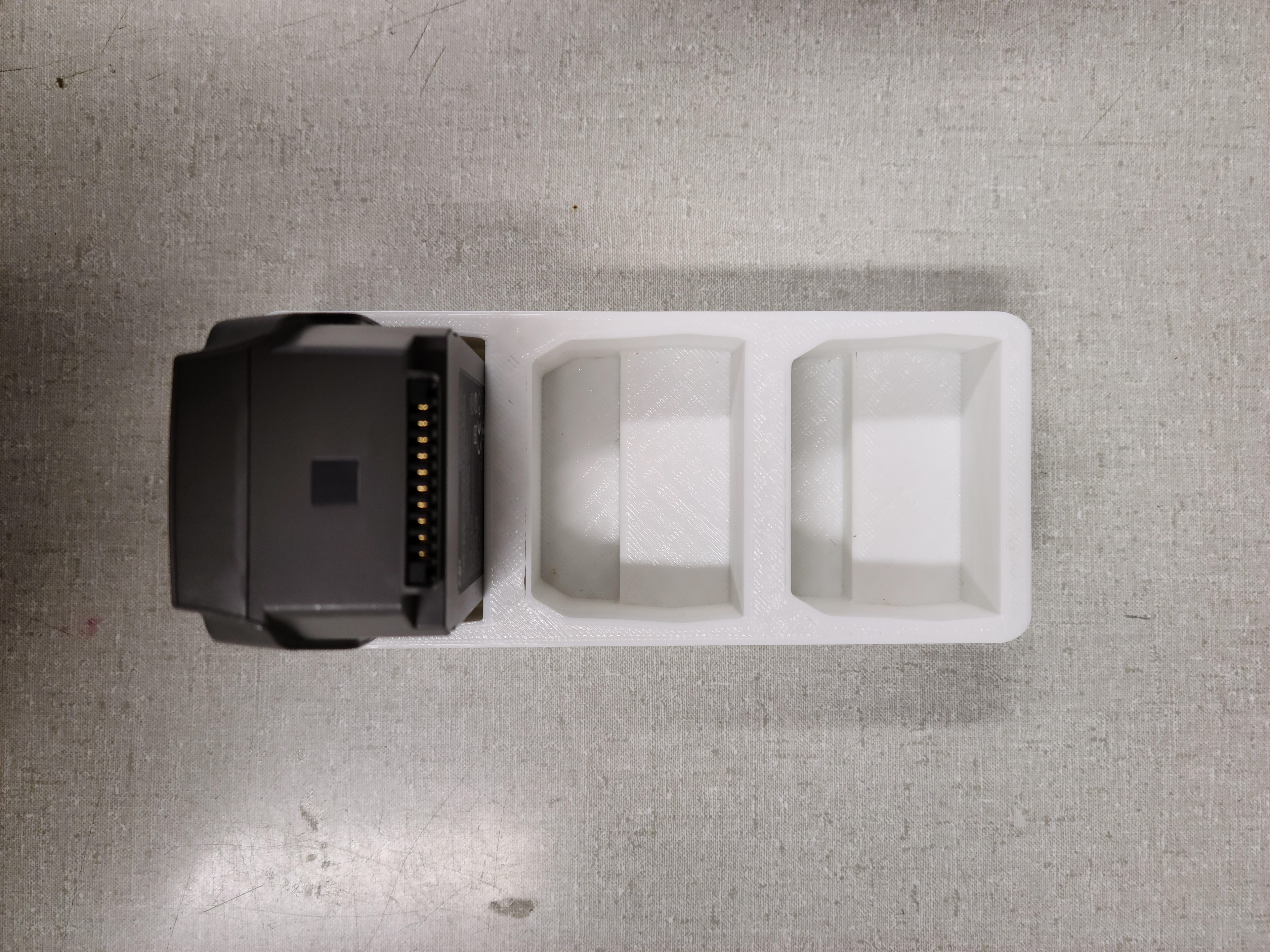
The first print turned out very good. The batteries fit well, showing that the holder was scaled properly. The next step was to create a holder with more than the initial 3 slots that were designated with the original file. Here in the UAS program we have 16 Mavic 2 Pro batteries. So ideally a single large holder would hold all the batteries. I began by creating a large base that fit as large of a printing area allowed by our 3D printer, and taken the scaled lots and placing as many as I could fit, into it. This lead to me only being able to fit 12 slots (3 by 4 design). This design was going to take over a day to print, and was going to use a vast amount of filament. Weldon suggested trying another prototype creation, that used less overall material by slimming the dividers, and removing the bottom base of the holder, since it would always be resting on a table. So I created a new one with these ideas in mind and printed it. This new print however, got scaled wrong in the process and did not properly fit, so I had to scale it again. After printing this third prototype, it fit the batteries, was as stable as the original, and used thirty-three percent less filament.
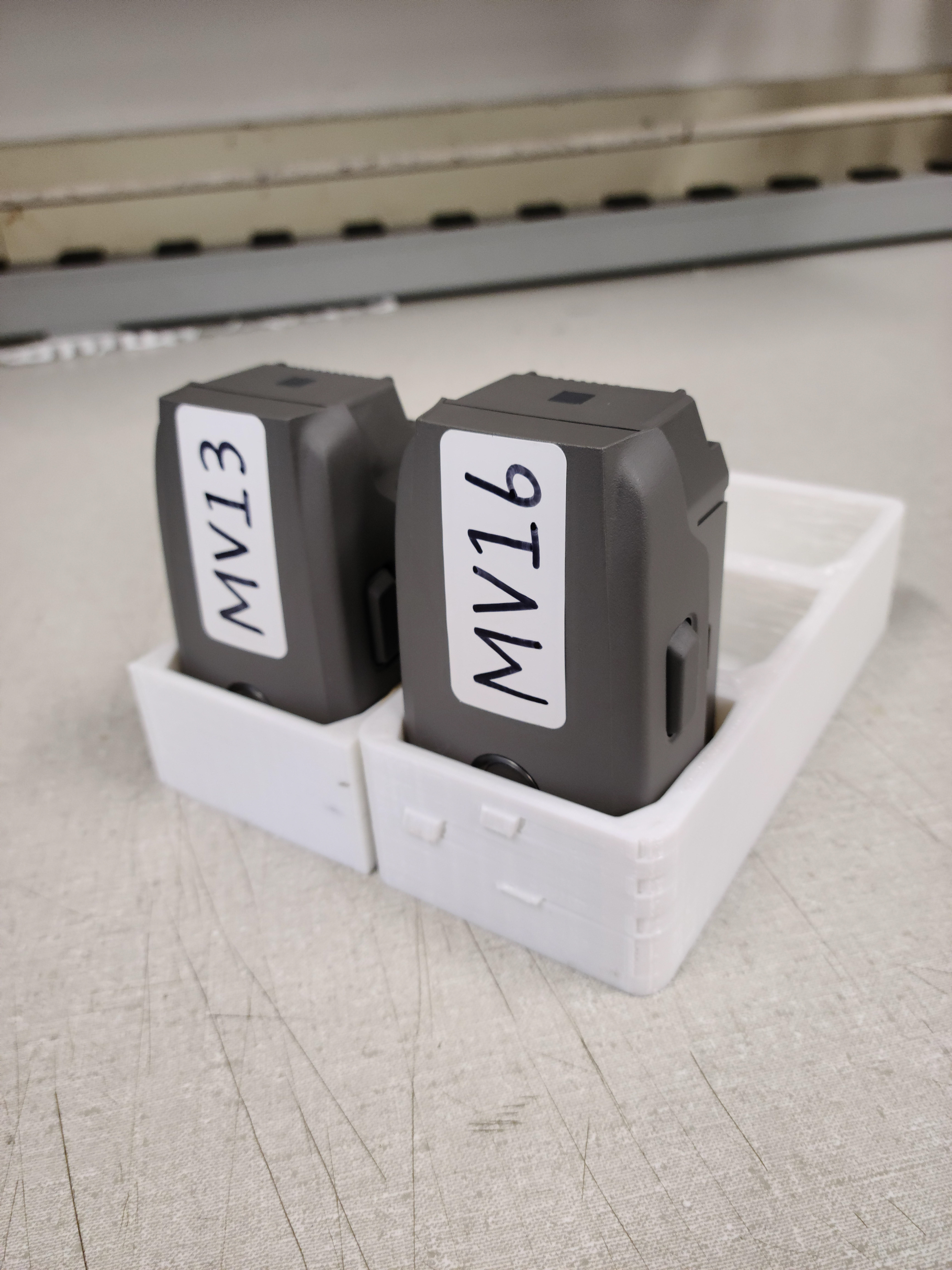
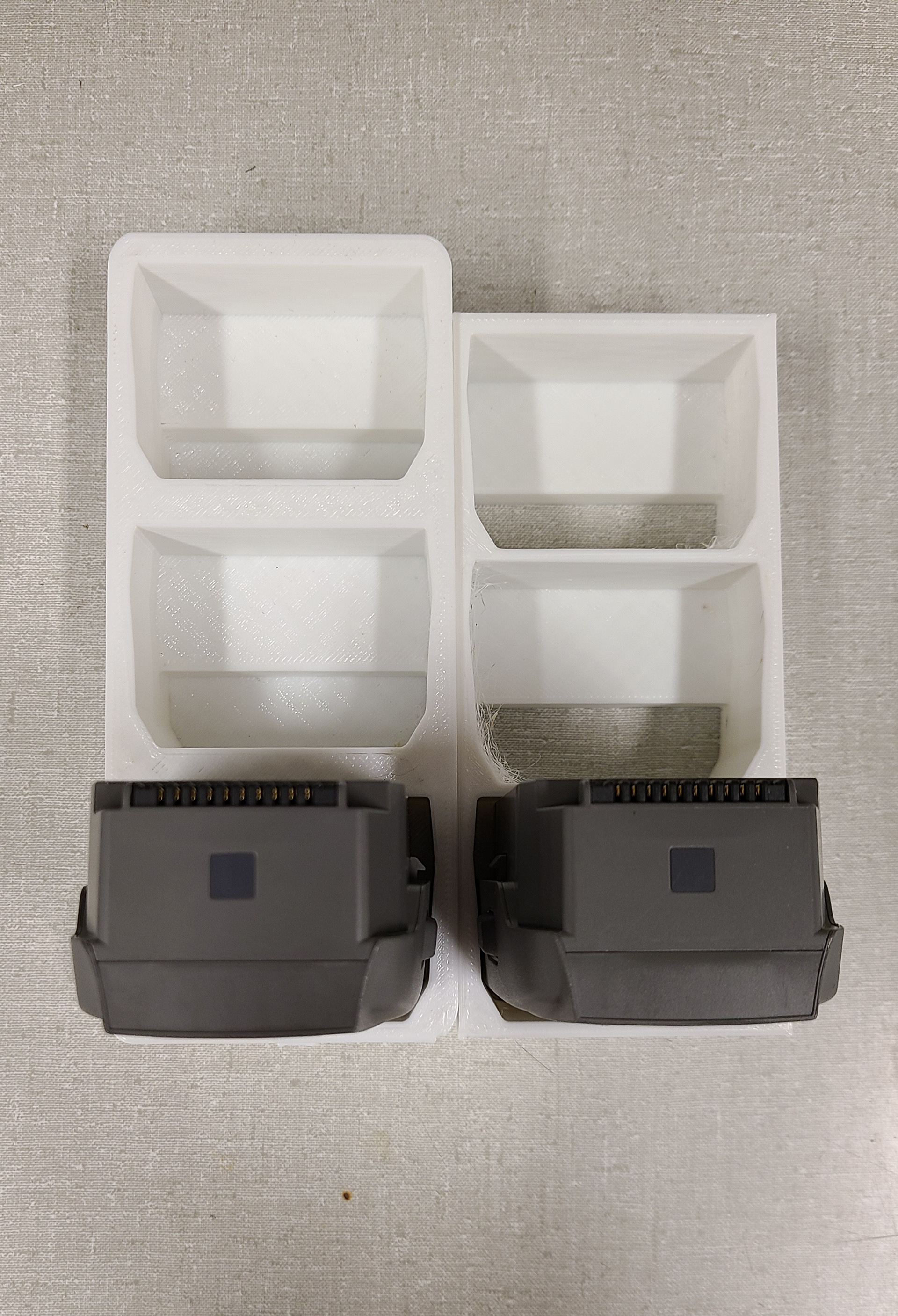
With this new design I applied its characteristics to the larger version. The larger version also saw the addition of connectors so that the additional battery holders that will be needed for this project, would all be able to connect together, improving stability. This new version used roughly half the amount of the original large holder design and would take 6 hours less to print. I loaded this model into Cura and set the printer up for this print. It still was a high-speed print, but this time it needed some printed supports for the connectors. The gcode file was then loaded into the printer and left to print overnight. The next morning the print was completed. The batteries fit into all of the slots; however, the supports did not quite print how they needed. The connectors at the time still looked like they would work, and later would be found to still function properly.
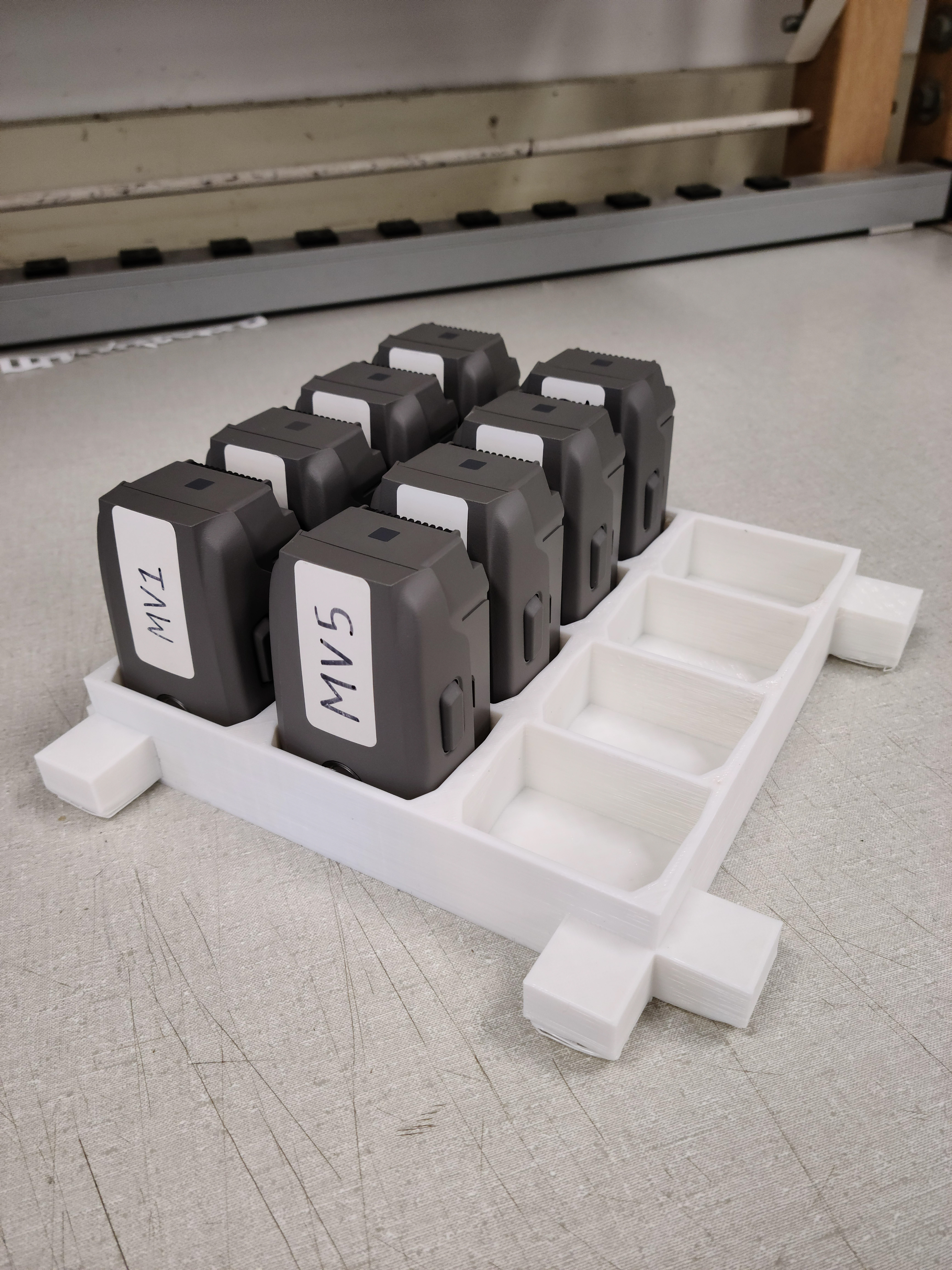
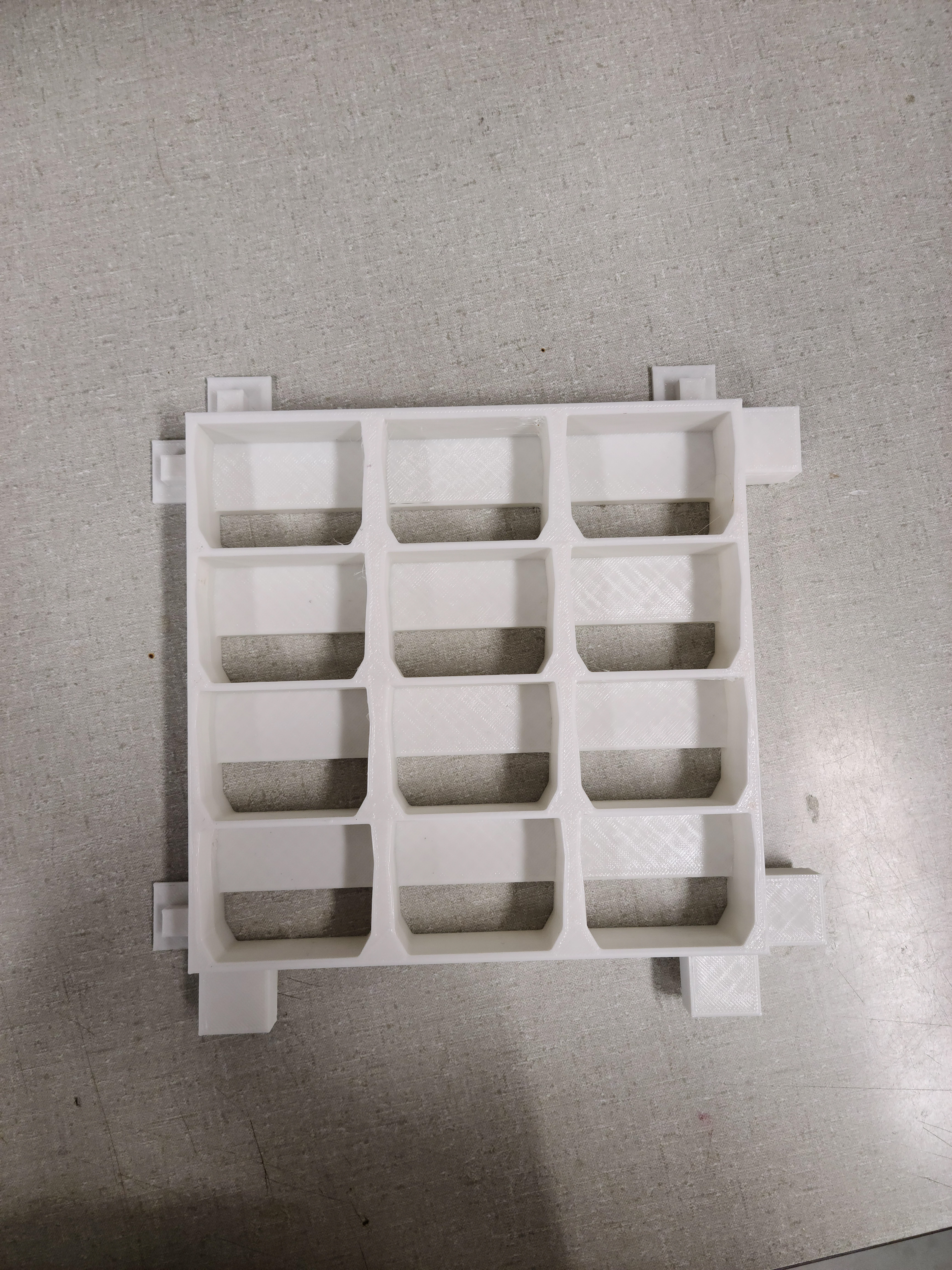
The next thing was to create an add-on for the remaining Mavic 2 Pro batteries. So, based on the third prototype, I expanded it to fit 4 batteries, and added connectors so that it would connect properly with its larger counterpart. This time when loading the model into Cura, I fixed the settings for printing the supports so that they would come out as originally intended, while still working with the slightly distorted ones on the first print. It was printed successfully and connected perfectly with the larger one. Now that the Mavic 2 Pro batteries had a home, it was time to work on the M210 aircraft and controller batteries.
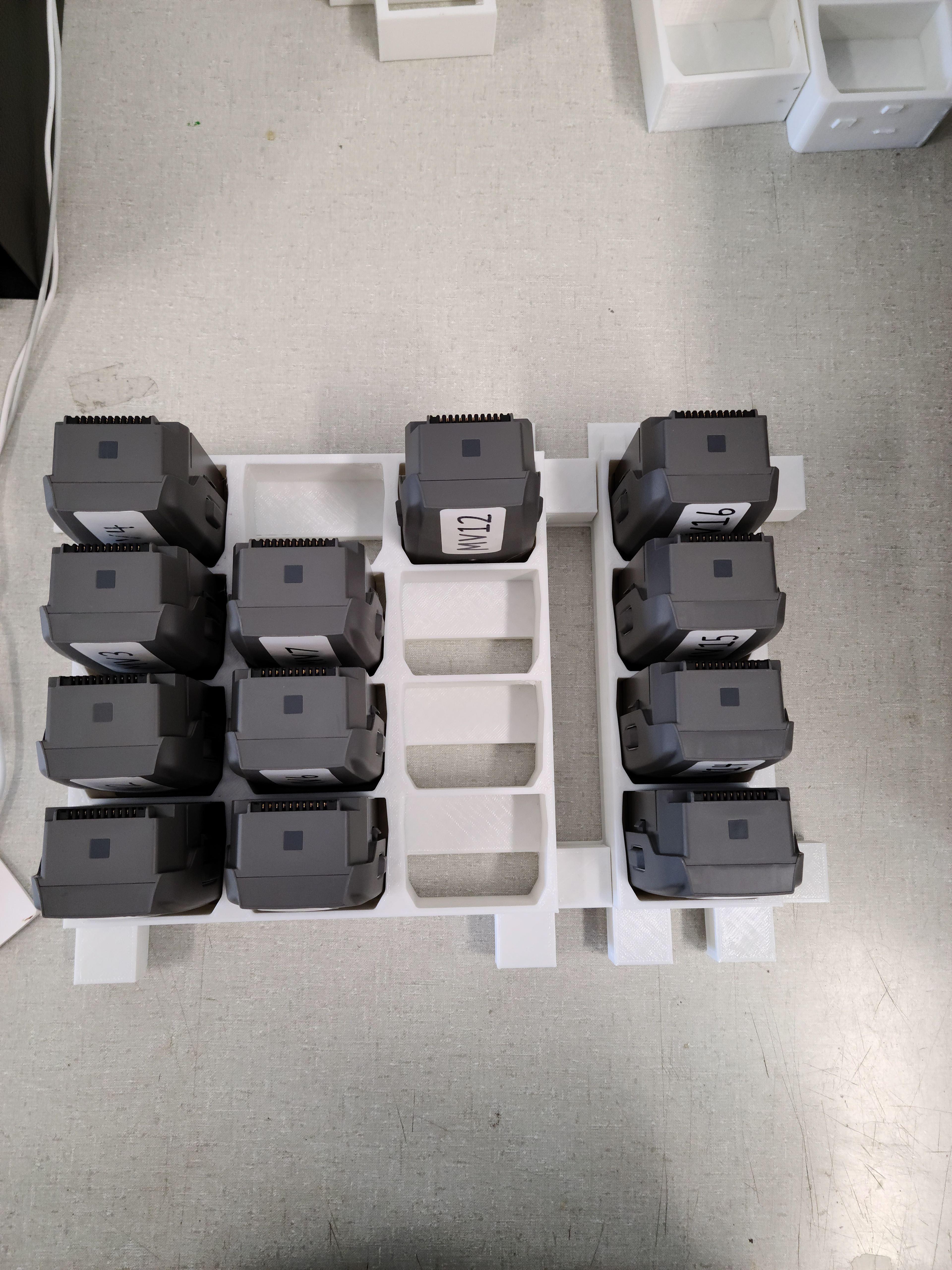
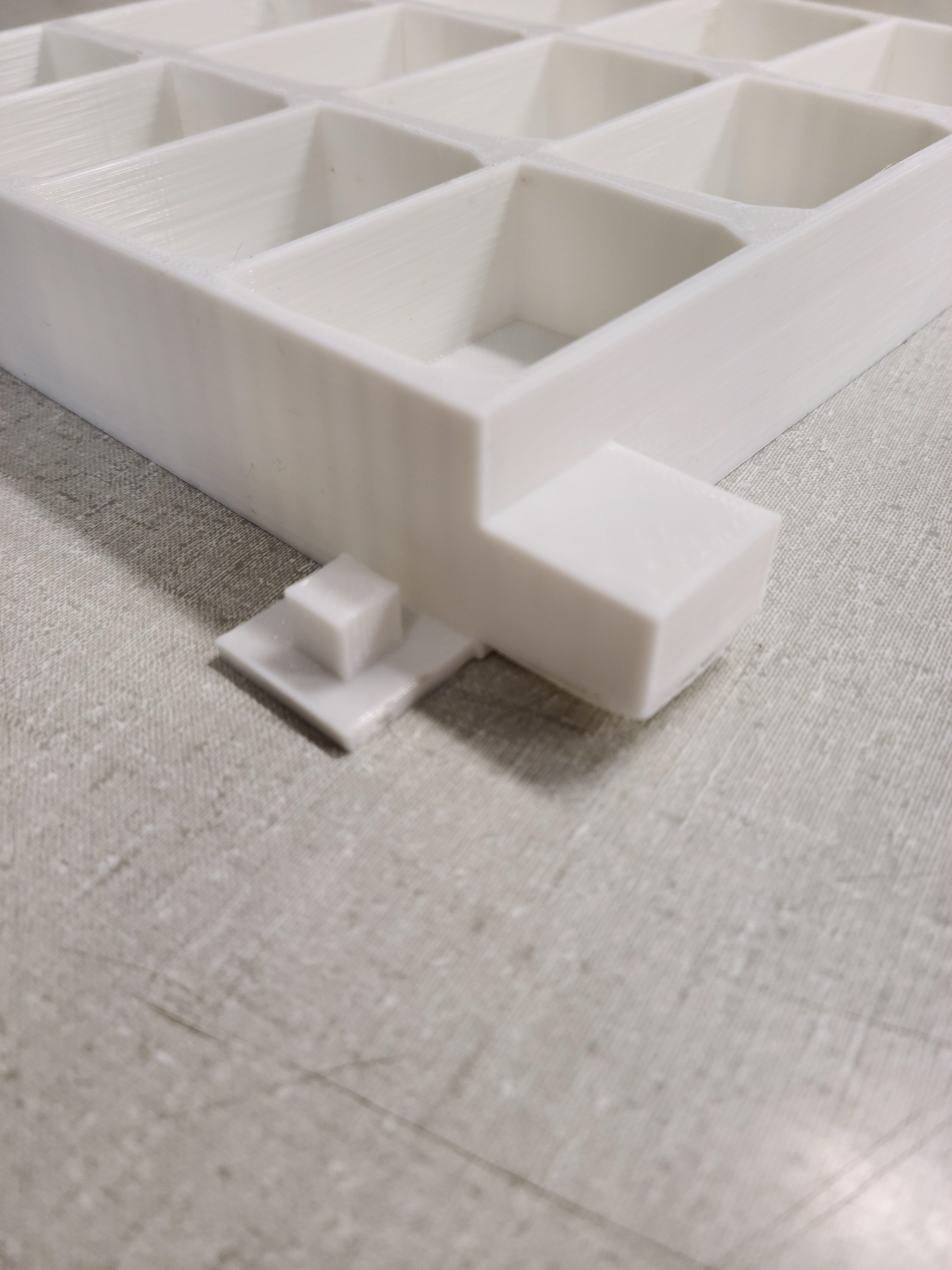
After a quick look on the internet, I could find no holder for these batteries that I could base my holder off of. So, this holder was going to be completely designed by myself. I started by measuring the dimensions of both the aircraft and controller batteries. From there I prototyped a small holder that could hold one just one M210 aircraft, and one controller battery. This was to make sure my measurements were correct. This was then printed and found that while the controller battery slot was the correct size, the aircraft battery slot was a bit too small. With these adjustments in mind, I began work on the larger holder. This holder would use the same base size as the Mavic 2 Pro holder, to ensure the connectors would be in line. This holder for the M210 batteries was designed to hold four aircraft battery, and six controller batteries. This was decided as the lab only has six controller batteries, so all could be kept in the same row. This model was then loaded into Cura and left to print overnight. The next day it was complete, the holders were found to all be the correct size and connected well with the Mavic 2 Pro holders.
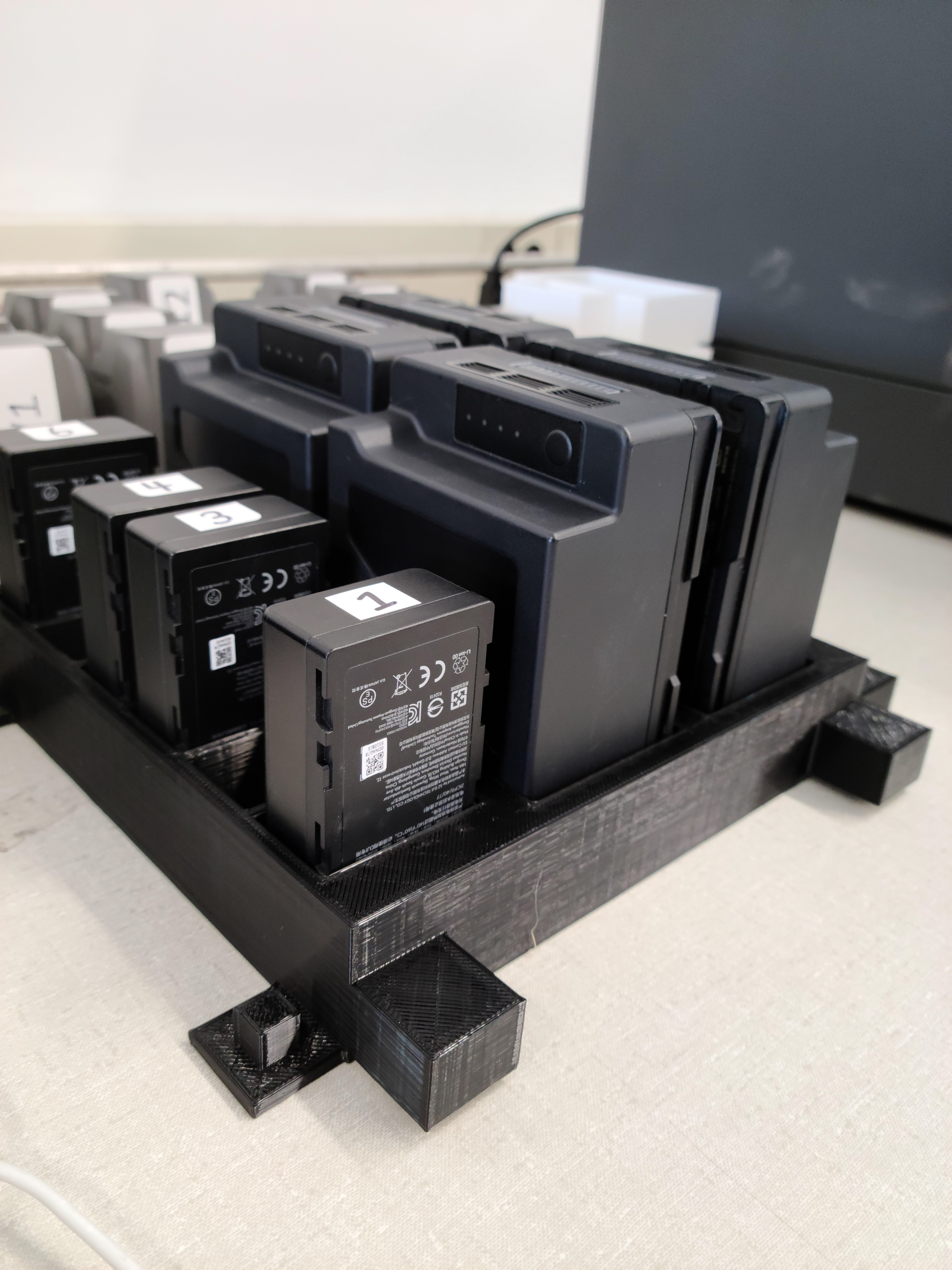
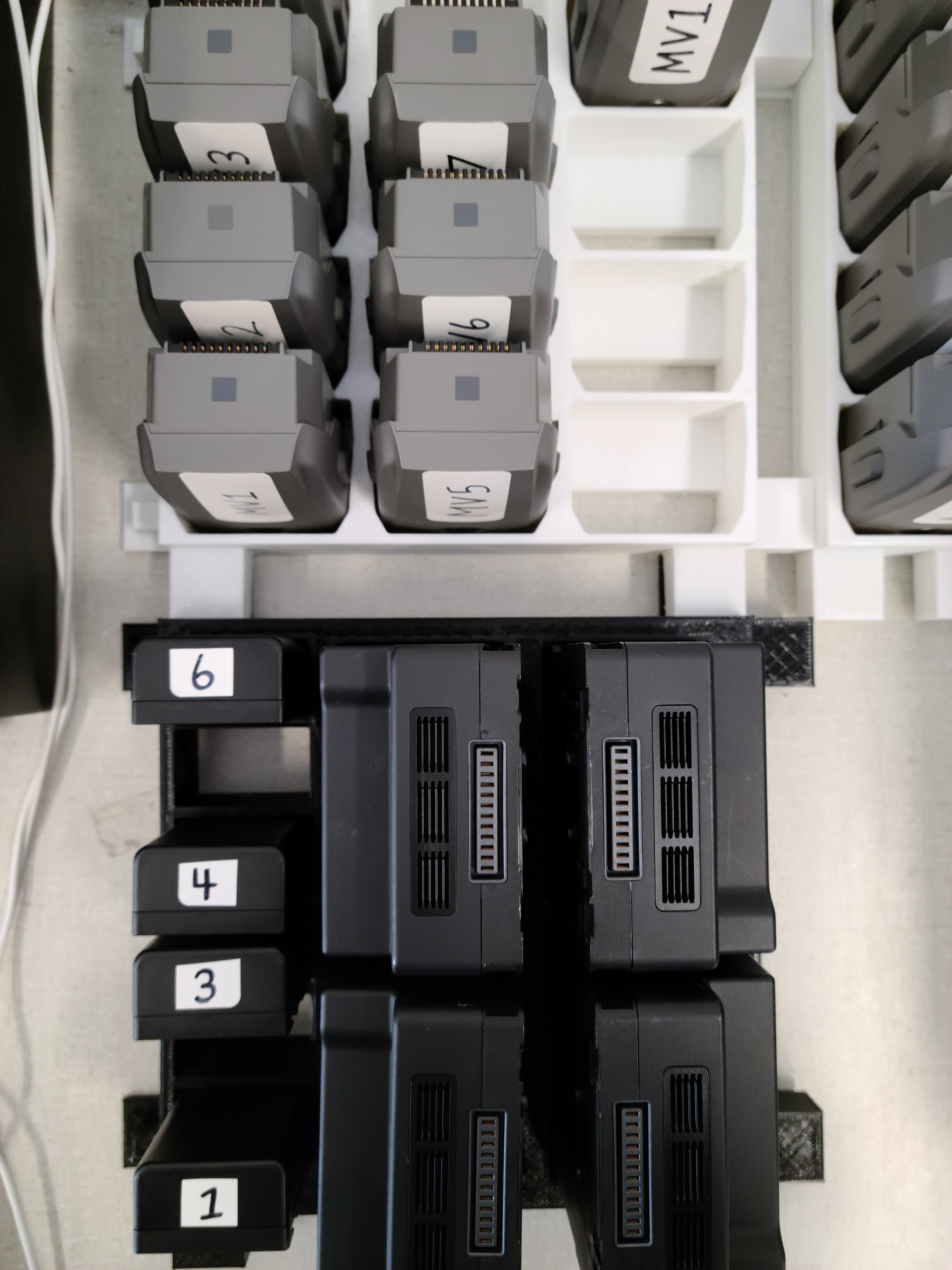
There remained six M210 aircraft batteries that needed a holder. For them, I simply removed the controller battery slots from the holder and placed two more aircraft battery slots in their place. This new design was exported and printed over Christmas. Upon coming back, the print was found completed, and fit just as well as all the other holders. This would complete my journey of rapid prototyping 3D printed holders for these smart batteries.
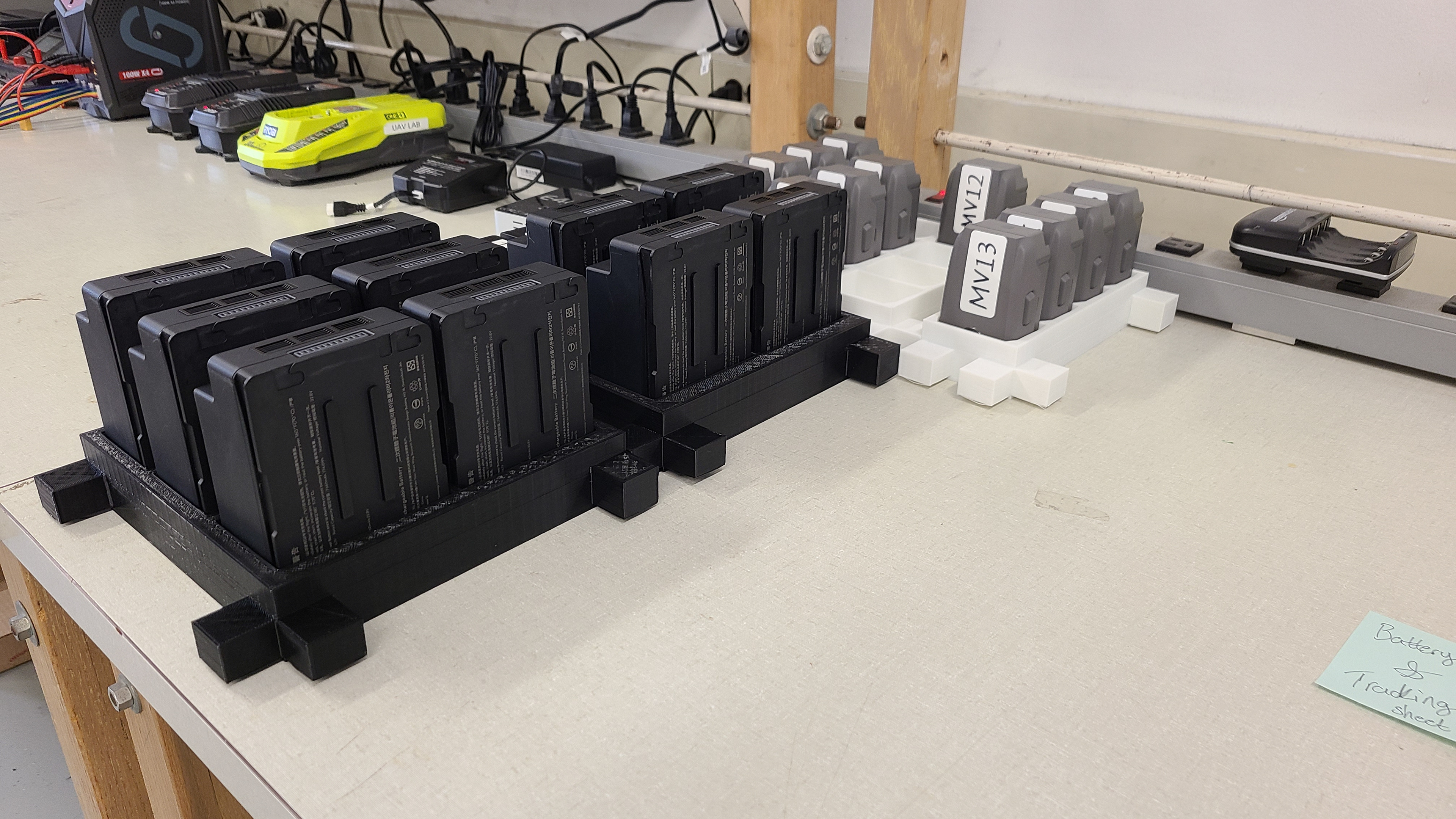
Over the roughly two-week period, I learned a lot about rapid prototyping, 3D modeling, and 3D printing. These skills are useful in the field of UAS as you can 3D print components for aircraft and develop new components that would be improved in comparison to what is currently available. Especially with the ability to rapidly prototype designs and try them out in their intended environments, with no need to wait for things to be shipped. With this entry level experience under my belt, I now understand the basics of all of these skills, which I intend, in the future, to further my understanding of.